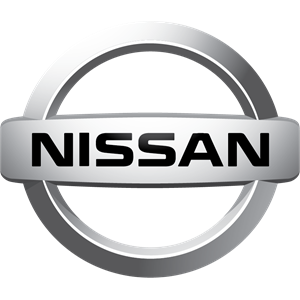
Nissan Versa
Sedan Service Manual
Engine » Engine mechanical (EM) » Cylinder block
Inspection
CRANKSHAFT END PLAY
- Measure the clearance between thrust bearings and crankshaft
arm when crankshaft is moved fully forward or backward with a
suitable tool (A).
- If the measured value exceeds the limit, replace thrust bearings,
and measure again. If it still exceeds the limit, replace crankshaft
also.

CONNECTING ROD SIDE CLEARANCE
- Measure the side clearance between connecting rod and crankshaft
arm with a suitable tool (A).
- If the measured value exceeds the limit, replace connecting rod,
and measure again. If it still exceeds the limit, replace crankshaft
also.
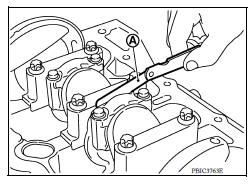
PISTON TO PISTON PIN OIL CLEARANCE
Piston Pin Hole Diameter
Measure the inner diameter of piston pin hole with an suitable tool
(A).
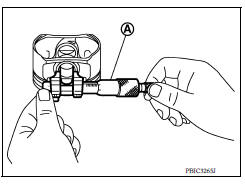
Piston Pin Outer Diameter
Measure the outer diameter of piston pin with a suitable tool (A).
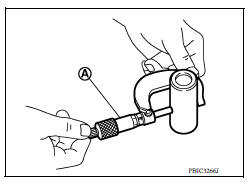
Piston to Piston Pin Oil Clearance
(Piston to piston pin oil clearance) = (Piston pin hole diameter) - (Piston pin
outer diameter)
- If oil clearance is out of the standard, replace piston and piston pin
assembly.
- When replacing piston and piston pin assembly.
NOTE:
- Piston is available together with piston pin as assembly.
- Piston pin (piston pin hole) grade is provided only for the parts
installed at the factory. For service parts, no
grades can be selected. Only grade "0" is available.
PISTON RING SIDE CLEARANCE
- Measure the side clearance of piston ring and piston ring groove
with a suitable tool (A).
- If the measured value exceeds the limit, replace piston ring, and
measure again. If it still exceeds the limit, replace piston also.
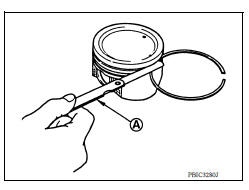
PISTON RING END GAP
- Check that cylinder bore inner diameter is within specification. Refer
to "PISTON TO CYLINDER BORE
CLEARANCE".
- Lubricate piston (1) and piston ring (2) with new engine oil and
then insert (A) piston ring until middle of cylinder (B) with piston,
and measure piston ring end gap with a feeler gauge (C).
- If the measured value exceeds the limit, replace piston ring, and
measure again. If it still exceeds the limit, replace cylinder block.
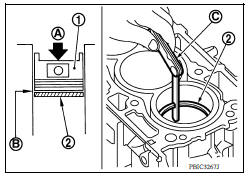
CONNECTING ROD BEND AND TORSION
- Check with a connecting rod aligner.
(A) : Bend
(B) : Torsion
(C) : Feeler gauge
- If it exceeds the limit, replace connecting rod assembly.
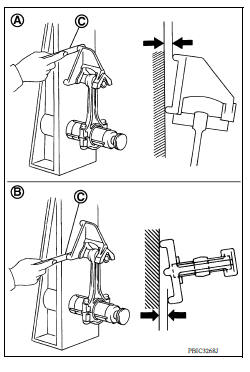
CONNECTING ROD BIG END DIAMETER
- Install connecting rod cap (1) without connecting rod bearing
installed, and tightening connecting rod cap bolts to the specified
torque.
(2) : Connecting rod
(A) : Example
(B) : Measuring direction of inner diameter
- Measure the inner diameter (B) of connecting rod big end with a
suitable tool.
- If out of the standard, replace connecting rod assembly.
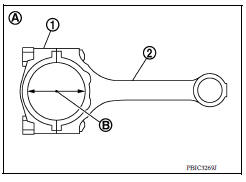
CONNECTING ROD BUSHING OIL CLEARANCE
Connecting Rod Bushing Inner Diameter
Measure the inner diameter of connecting rod bushing with a suitable
tool (A).
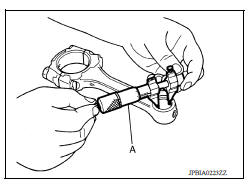
Piston Pin Outer Diameter
Measure the outer diameter of piston pin with a micrometer (A).
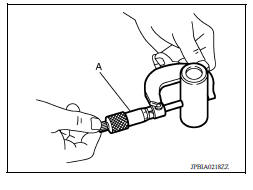
Connecting Rod Bushing Oil Clearance
(Connecting rod bushing oil clearance) = (Connecting rod bushing inner diameter)
- (Piston pin outer diameter)
- If the measured value is out of the standard range, replace connecting
rod assembly and/or piston and piston
pin assembly.
- If replacing piston and piston pin assembly.
- If replacing connecting rod assembly.
CYLINDER BLOCK TOP SURFACE DISTORTION
- Using a scraper, remove gasket on the cylinder block surface, and also
remove engine oil, scale, carbon, or
other contamination.
CAUTION:
Be careful not to allow gasket particles to enter engine oil or engine
coolant passages.
- Measure the distortion on the cylinder block upper face at different
points in six directions with a suitable tool (A) and (B).
- If it exceeds the limit, replace cylinder block.
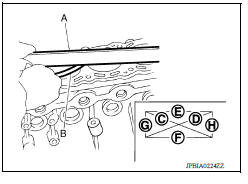
MAIN BEARING HOUSING INNER DIAMETER
- Install main bearing cap without main bearings installed, and tighten
main bearing cap bolts to the specified
torque.
- Measure the inner diameter of main bearing housing with a suitable tool.
- Measure the position shown [5 mm (0.20 in)] backward from main
bearing housing front side in the 2 directions as shown. The
smaller one is the measured value.
(1) : Cylinder block
(2) : Main bearing cap
: Engine front
- If out of the standard, replace cylinder block and main bearing
caps assembly.
NOTE:
Main bearing caps cannot be replaced individually, because they are
machined together with cylinder block.
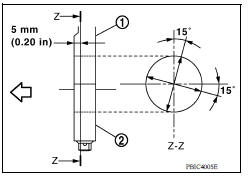
PISTON TO CYLINDER BORE CLEARANCE
Cylinder Bore Inner Diameter
- Using a suitable tool, measure the cylinder bore for wear, outofround
and taper at six different points on each cylinder. [(A) and (B)
directions at (C), (D), and (E)] [(A) is in longitudinal direction of
engine]
(f) : 10 mm (0.39 in)
(g) : 60 mm (2.36 in)
(h) : 124 mm (4.88 in)
NOTE:
When determining cylinder bore grade, measure the cylinder bore
(B) direction at (D) position.
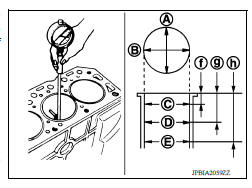
- If the measured value exceeds the limit, or if there are scratches
and/or seizure on the cylinder inner wall,
replace cylinder block.
NOTE:
Oversize piston is not available.
Piston Skirt Diameter
Measure the outer diameter of piston skirt with a suitable tool (A).
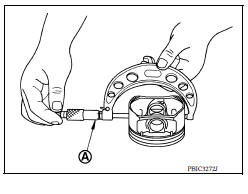
Piston to Cylinder Bore Clearance
Calculate by piston skirt diameter and cylinder bore inner diameter
[direction (B), position (D)].
(A) : Direction A
(C) : Position C
(E) : Position E
(f) : 10 mm (0.39 in)
(g) : 60 mm (2.36 in)
(h) : 124 mm (4.88 in)
(Clearance) = (Cylinder bore inner diameter) - (Piston skirt diameter)
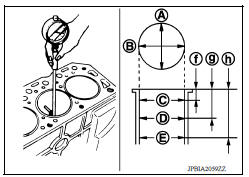
- If it exceeds the limit, replace piston and piston pin assembly and/or
cylinder block.
CRANKSHAFT MAIN JOURNAL DIAMETER
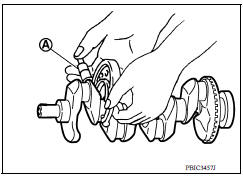
CRANKSHAFT PIN JOURNAL DIAMETER
- Measure the outer diameter of crankshaft pin journal with a suitable
tool.
- If out of the standard, measure the connecting rod bearing oil
clearance.
OUTOFROUND AND TAPER OF CRANKSHAFT
-
Measure the dimensions at four different points as shown on
each
main journal and pin journal with a suitable tool.
-
Outofround is indicated by the difference in dimensions
between
(a) and (b) at (c) and (d).
-
Taper is indicated by the difference in dimension between
(c) and
(d) at (a) and (b).
-
If the measured value exceeds the limit, correct or replace
crankshaft.
-
If corrected, measure the bearing oil clearance of the
corrected main journal and/or pin journal. Then select
main bearing and/or connecting rod bearing.
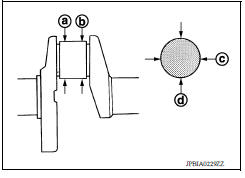
CRANKSHAFT RUNOUT
- Place a Vblock on a precise flat table to support the journals on both
ends of the crankshaft.
- Place a suitable tool (A) straight up on the No. 3 journal.
- While rotating crankshaft, read the movement of the pointer on the
suitable tool. (Total indicator reading)
- If it exceeds the limit, replace crankshaft.
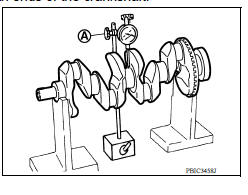
CONNECTING ROD BEARING OIL CLEARANCE
Method by Calculation
- Install connecting rod bearings (2) to connecting rod (3) and connecting
rod cap (1), and tighten connecting rod cap bolts to the
specified torque.
(A) : Example
(B) : Inner diameter measuring direction
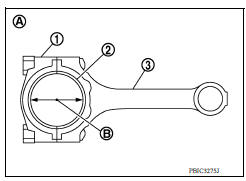
- If clearance exceeds the limit, select proper connecting rod bearing
according to connecting rod big end
diameter and crankshaft pin journal diameter to obtain specified bearing oil
clearance.
Method of Using Plastigage
- Remove engine oil and dust on crankshaft pin and the surfaces of each
bearing completely.
- Cut a plastigage slightly shorter than the bearing width, and place it
in crankshaft axial direction, avoiding oil
holes.
- Install connecting rod bearings to connecting rod and cap, and tighten
connecting rod cap bolts to the specified
torque.
CAUTION:
Do not rotate crankshaft.
- Remove connecting rod cap and bearing, and using the scale (A)
on the plastigage bag, measure the plastigage width.
NOTE:
The procedure when the measured value exceeds the limit is
same as that described in the "Method by Calculation".
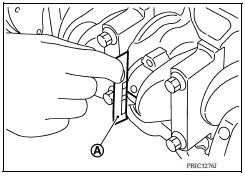
MAIN BEARING OIL CLEARANCE
Method by Calculation
- Install main bearings (3) to cylinder block (1) and main bearing cap
(2), and tighten main bearing cap bolts to the specified torque.
(A) : Example
(B) : Inner diameter measuring direction

Method of Using Plastigage
- Remove engine oil and dust on crankshaft main journal and the surfaces
of each bearing completely.
- Cut a plastigage slightly shorter than the bearing width, and place it
in crankshaft axial direction, avoiding oil
holes.
- Install main bearings to cylinder block and main bearing cap, and
tighten main bearing cap bolts to the specified
torque.
CAUTION:
Do not rotate crankshaft.
- Remove main bearing cap and bearings, and using the scale (A)
on the plastigage bag, measure the plastigage width.
NOTE:
The procedure when the measured value exceeds the limit is
same as that described in the "Method by Calculation".
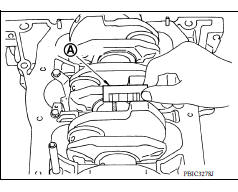
MAIN BEARING CRUSH HEIGHT
- When main bearing cap is removed after being tightened to the
specified torque with main bearings (1) installed, the tip end of
bearing must protrude (B).
(A) : Example
Standard : There must be crush height.
- If the standard is not met, replace main bearings.
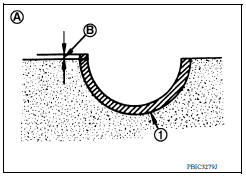
CONNECTING ROD BEARING CRUSH HEIGHT
- When connecting rod cap is removed after being tightened to the
specified torque with connecting rod bearings (1) installed, the tip
end of bearing must protrude (B).
(A) : Example
Standard : There must be crush height.
- If the standard is not met, replace connecting rod bearings.
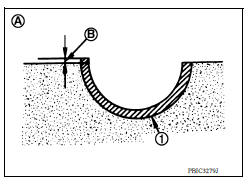
MAIN BEARING CAP BOLT OUTER DIAMETER
- Measure the outer diameters (d1) and (d2) at two positions as
shown.
(A) : (d1) measuring position
(B) : (d2) measuring position
- If reduction appears in places other than (B) range, regard it as
(d2).
Limit [(d1) - (d2)]: 0.2 mm (0.0078 in)
- If it exceeds the limit (a large difference in dimensions), replace
main bearing cap bolt with a new one.
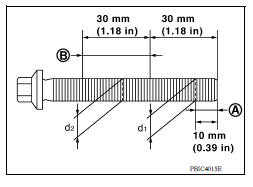
CONNECTING ROD CAP BOLT OUTER DIAMETER
- Measure the outer diameter (d) at position as shown.
- If reduction appears in a position other than (d), regard it
Limit: 7.75 mm (0.3051 in)
- When (d) is less than the limit (when it becomes thinner), replace
connecting rod cap bolt with a new one.
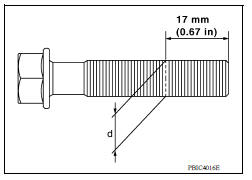
FLYWHEEL DEFLECTION (M/T models)
- Measure the deflection of flywheel contact surface to torque with a
suitable tool (A).
- Measure the deflection at 210 mm (8.27 in) diameter.
Limit : 0.45 mm (0.0177 in) or less.
- If measured value is out of the standard, replace flywheel.
- If a trace of burn or discoloration is found on the surface, clean it
with sandpaper.
CAUTION:
When measuring, keep magnetic fields (such as dial indicator
stand) away from signal plate of the rear end of crankshaft.
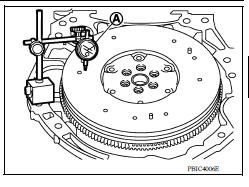
More about «Cylinder block»:
Inspection